11 Trusted BAS Alternatives in 2024
BAS encompass a rich history dating back to the 1600s, evolving from manual controls to sophisticated modern systems like ABB’s Aspect for efficient HVAC regulation. Tridium’s Niagara framework leads in global control integration. Expect future BAS to excel in scalability and energy efficiency.
Alternatives to BAS cover a broad spectrum, including DCS, SCADA, PLC, ICS, RTU, DAS, IoT, ERP, MES, OPC, MQTT.
DCS
The Distributed Control System (DCS) is an automated control network aimed at centralizing supervision while distributing functionalities across various elements. Predominantly used in emerging process industries, it leverages the decentralized control principle.
DCS Top Features
- Versatility: DCS covers managing and controlling processes across a myriad of industries.
- Distributed Intelligence: The control, monitoring, and reporting components are well distributed in process plants.
- Scalability: DCS can support significant modifications, upgrades, and integration to existing industry structures.
- Resilience: Its structure significantly reduces the risk of single processor failure effects.
Feature | Description |
---|---|
Set Configuration Tools | These include database management, control logic, graphics, and system security tools. |
Efficiency | Optimization of interaction among numerous controllers, enhancing production efficiency. |
Safety | Improvement of safety measures during the entire plant life cycle. |
DCS Downsides
- DCS systems may pose higher upfront installation costs despite reducing operational expenditures in the long run.
- Not suitable for small-scale, real-time operations where PLC is more ideal.
DCS Use Cases
Use case 1 – Power Generation
DCS is integral in power generation industries. Its ability to centralize control and distribute functionalities bolsters efficiency.
Use case 2 – Oil and Gas Industry
Within the oil and gas industry, DCS helps manage safety-critical applications smoothly, and enhances operational effectiveness.
Use case 3 – Biotech and Pharmaceuticals
Biotech and pharmaceutical industries thrive on precision, where DCS comes into play by enabling superior control and reporting.
SCADA
Supervisory Control and Data Acquisition (SCADA) is a computer application that provides centralized monitoring and control for a complete network. It is engineered to automate complex industrial processes and can efficiently detect and correct problems while enabling assessment of trends over time.
SCADA Top Features
- Automation of complex industrial processes which enables more efficient and control systems
- Ability to collect and process real-time data from diverse sources.
- Components include RTU, PLCs, and discrete sensors for data gathering and control as well as HMI for user interaction.
- Advanced communication capabilities over Ethernet or IPs.
Feature | Benefit |
---|---|
SQL Databases | Enables rapid data retrieval and storage |
Interoperability | Aids in seamless integration with different systems. |
Scalability | Supports system growth and complexity over time. |
SCADA Downsides
- While SCADA facilitates seamless automation, installing and maintaining the system can be cost-intensive.
- Legacy systems have limited support and lack features like scalability and interoperability.
- Increasingly connected systems heighten cybersecurity
concerns.
SCADA Use Cases
Use case 1: Industrial plants
In industrial plants, SCADA can effectively automate and control complex processes, reducing error margins and increasing efficiency.
Use case 2: Oil and gas refining
SCADA systems prove instrumental in the oil and gas sector for real-time data monitoring and processing, facilitating safe and optimal operation.
Use case 3: Transportation
In the transportation industry, SCADA supports efficient monitoring and controlling of systems, fostering operational improvements and better safety measures.
MQTT
MQTT or Message Queuing Telemetry Transport is an ISO standard (ISO/IEC PRF 20922) protocol engineered for networks with low-bandwidth and high latency. Originating in the oil and gas domain, now it’s largely leveraged in IIoT, IoT, consumer and enterprise applications, thanks to the evolution in digital services, mobile capabilities, remote access, and edge computing.
MQTT Top Features
- Architecture: Publish-subscribe format decoupling data-producing hardware from data-consuming software.
- Security: Enhanced with modern authentication protocols like OAuth, TLS1.3, Customer Managed Certificates.
- Scalability: Accommodates millions of low-power device connections over low-bandwidth networks.
- Language Support: Backed by languages like Python, ensuring easy implementation using minimal coding.
- Sparkplug: An additional specification enhancing MQTT for critical applications with standard topic namespace, enhanced state management, and data-rich payload.
Feature | Function |
---|---|
Multisite SCADA | Facilitates remote data collection in hydraulic fracturing operations. |
Security Measures | Compatible with firewalls, VPNs, IPsec protecting IoT systems. |
WSS Envelope | Enables data reception directly into a web browser. |
MQTT Limitations
- Primarily developed for low-bandwidth, high latency networks, might not be efficient for high-speed, low-latency network environments.
- Not every implementation supports all features of the MQTT specification, leading to potential compatibility issues.
MQTT Use Cases
Use Case 1: Industrial Automation
MQTT augments industrial automation capabilities, allowing for efficient, secure data integration and improved remote accessibility.
Use Case 2: AWS IoT Core
Connected with AWS IoT Core, MQTT facilitates routing of trillions of messages and connection of billions of IoT devices to AWS services.
Use Case 3: Smart City PoC Design
MQTT serves as a robust messaging transport in the design of smart city proof-of-concepts, thus advancing urban technological evolution.
PLC
Invented in the 1960s to replace hardwired relays and timers, Programmable Logic Controllers (PLCs) are now a fundamental pillar in modern manufacturing processes. Today’s PLCs, defined by NEMA as ‘Digitally operating electronic apparatus with a programmable memory’, boast advanced capabilities courtesy of breakthroughs in processor and memory technology.
PLC Top Features
- Compactness and Speed: Well beyond their suitcase-sized predecessors, current PLCs operate at swift speeds and showcase advanced capabilities that continue to pave the way for big data and AI on the factory floor.
- Standardization: The introduction of the IEC 61131-3 Standard resulted in standardized PLC functions, inputs, and outputs, simplifying programming language understanding.
- Integration: Modern PLCs seamlessly integrate with systems like ERP, MES systems, and SCADA, enhancing efficiency and overall performance of manufacturing operations.
Advanced Feature | Description |
---|---|
Visual System Integration | An enabling feature for more user-friendly interfaces by allowing PLCs to share information. |
Motion Control | A crucial component for controlling machine movements throughout various industrial operations. |
Support for Multiple Communication Protocols | Augments the ability of PLCs to operate across diverse platforms, increasing adaptability. |
PLC Limitations
- Troubleshooting complexity: Although presenting an array of benefits, PLCs can be challenging to troubleshoot.
- Skilled Workforce Requirement: Effective use of PLCs relies on a workforce proficient in operating these sophisticated systems.
PLC Use Cases
Use case 1: Robotic Arm Control In Automotives
PLC’s advanced programming languages and motion control capabilities make it an ideal solution for controlling robotic arms in the automotive production line.
Use case 2: Airport Runway Control
Airport runway lighting and traffic control systems can be efficiently managed with PLC, offering reliable, real-time control of time-critical operations.
Use case 3: Textile Equipment
PLCs, with their addition of HMIs in the 1990s, have emerged as essential tools within the textile industry, managing complex processes and machinery to boost production efficiency.
ICS
As the backbone of industrial operations and automation, the Industrial Control System (ICS) amalgamates various devices, systems, controls, and networks. ICS finds its niche in several key industries like manufacturing, transportation, energy, and water treatment.
ICS Top Features
- Comprehensive Environment: ICS encompasses a vast array of components such as IT & Operational Technology (OT) variables, PLC, RTU, HMI, Control and SCADA Servers, and Intelligent Electronic Device (IED). It also includes the Data Historian, the Control Loop, solidifying its holistic approach.
- Variants for Different Needs: ICS includes both Supervisory Control and Data Acquisition (SCADA) and Distributed Control Systems (DCS). While SCADA is ideal for long-distance monitoring and control, DCS is excellent for supervising localized production systems.
- Robust Communication Protocols: ICS uses several cutting-edge protocols including PROFIBUS, DNP3, Modbus, and OPC ensuring seamless data communication.
- IT/OT Convergence: This fusion creates superior integration and visibility across the supply chain, fostering efficient workflow.
System | Main Use |
---|---|
SCADA | Optimized for long-distance process monitoring and control. |
DCS | Perfect for controlling production systems within a single location. |
ICS Disadvantages
- Target for Cyberattacks: The convergence of IT and OT creates larger attack surfaces, making ICS vulnerable to sophisticated cyber threats.
- Rising Technology Risks: Emergence and adoption of new technologies like cloud computing, big data analytics, and IoT can compound the vulnerability, leaving ICS open to strategic attacks. Cases in point include the Stuxnet worm and BlackEnergy affecting significant facilities in Iran and Ukraine respectively.
ICS Use Cases
Use case 1: Manufacturing
With its integrated environment and robust communication protocols, ICS is ideal for fostering seamless operation and automation systems in manufacturing.
Use case 2: Power Generation
DCS, a component of ICS, shines in overseeing the intricate control systems within a specific location, making it indispensable for power generation plants.
Use case 3: Water Treatment
Long-distance process monitoring made possible by SCADA ensures efficient and effective management of water treatment processes across multiple sites.
RTU
The RTU or Remote Terminal Unit is a microprocessor-controlled electronic device that has created a critical link within control ecosystems, especially in challenging environments. It translates the language of objects in the real world to distributed control or SCADA systems, playing an essential role in various applications.
RTU Top Features
- Interface Functionality: Critical bridge between real-world objects and control systems.
- Resilience: Engineered to thrive in harsh conditions, and often solar-powered.
- Communication: Employs RS485 or wireless links to communicate with master systems.
- Programming Compatibility: Modern units adhere to the IEC 61131-3 standard for programmable logic controllers.
- Input/Output Cards: Fitted with AI, DI, DO/CO, and AO cards for varied applications.
- Multi-drop Scheme: Unique addressing allows multiple units to share a communications line.
- AC Power & Battery Backup: Ensures continuous operation during critical tasks.
- Autonomous Mode: Modern RTUs adapt based on physical override switches during maintenance.
Feature | Description |
---|---|
Monitoring | Analog inputs of different types provide robust and diverse monitoring capabilities. |
Data Translation | Ability to translate and scale raw data into relevant units for the user. |
RTU Limitations
- Wireless links can be affected by environmental factors and distance.
- Extensive features may require a learning curve for efficient use.
RTU Pricing
RTU models boast a range of price points, starting from $500 for entry-level models and extending up to $5,000 for premium models. The price correlates directly with the capacities, functionalities, and the reputation of the brand.
RTU Use Cases
Use Case 1: Pipeline and Grid Guarding Systems
In systems that monitor pipelines and grids, RTUs contribute to maintaining system efficacy and serve as a critical component to secure guard systems.
Use Case 2: Extreme Environments (e.g., Biosphere 2 project)
For projects conducted in extreme or remote locations, such as the Biosphere 2, RTUs are instrumental in linking isolated systems to a larger network, aiding in valuable data exchange.
Use Case 3: Industrial Applications
RTUs have seen wide usage globally in industries like oil and gas, electric, water utilities, refineries, food processing, and automobile manufacturing. Their flexibility and adaptability allow for diverse applications across sectors.
DAS
In the realm of digital control systems, DAS (Distributed Antenna System) presets a robust solution for poor in-building coverage, employing a complex network of small antennas as repeaters. This network connects to a central controller, further linked to the base station of a wireless carrier network. Let us traverse a deeper understanding of DAS, its core features, limitations, and profound use cases.
DAS Top Features
- Skilled at mitigating poor coverage within dense indoor spaces, making it fitting for establishments like shopping malls, medical centers, and high-rise buildings.
- Modular and versatile, it interfaces with any system for data recording and processing.
- Efficiently handles up to 240 analog or digital outputs.
- Reliable baud rate ranging from 150 to 38.4 kbaud, aligning with NASA’s serial data standard.
- Assisted by AIMOS (an inclusive DAS management platform) for seamless operations and maintenance.
Component | Description |
Unique address bus | Consists of 8 bits with 16 reserved for internal use, accommodating up to 240 distinct analog or digital inputs. |
Advanced frame setup | Includes 16 bit words sent continuously with a unique synchronization word to mark the inception of each data frame. |
AIMOS automation | Permits automatic operations with activities like alarm polling, RF frequency allocation, software updates, etc. These can be executed at specific or regular time intervals. It can also be integrated into third-party network management software. |
DAS Limitations
- Installation is labor-intensive, making DAS deployments a pricey affair.
- Inadequate visibility of the final costs, as DAS integrators can only provide ranges until a comprehensive site survey and RF benchmarking tests.
DAS Use Cases
High-density Habitats
DAS’s robust network of small antennas makes it ideal for densely populated indoor spaces. This could be shopping malls, high-rise buildings, and medical centers where connectivity is paramount.
Working with Multiple Carriers
While high in initial setup cost, DAS offers potential cost reduction by the possibility of being shared amongst multiple carriers.
Data Recording and Processing
This unique system is designed to interface with any experiment for data recording and processing. From small scale experiments to large scale deployments, DAS takes it all in its stride.
IoT
Probing the infinite mesh of the digital universe, we come upon a galaxy of interconnectivity termed as the Internet of Things (IoT). It conjures a network of devices, embellished with embedded sensors and potent software, radiating data across the vast cyberspace.
IoT Top Features
- Extensive Industrial Applicability: Transport, manufacturing, retail, healthcare—every realm mesmerised by its digital charm.
- Bifocal Accessibility: Brains offer local control, the connectivity enables external communication.
- Microcontroller Mastery: Serves as the brain, amalgamating microprocessor core, memory, input/output ports.
- Valued Services: Operational efficiency, new business model creation, generation of fresh revenue streams.
Control Interface: | Devices are linked, communication facilitated via intricate paths of I2C, SPI, CAN communication protocols. |
Versatility: | Devices varying in size, function, remote or co-located within larger systems. |
Smart Technology: | Smart manufacturing, cities, grids, logistics are catalysed, revolutionising traditional methods. |
IoT Disadvantages
- Complex Requirements: Microprocessors, memory size, operating voltage and current, I/O ports—each detail mandatory for an IoT microcontroller.
- Dependency: Reliance on multiple technologies like low-cost sensors, AI, machine learning, cloud computing for its functionality.
IoT Use Cases
Use case 1
IoT’s elegance gracefully entwines with the realm of automotive industry. Connected cars, enabled for device-to-device communication, redefine the industry’s landscape, facilitating continuous customer relationship and remote operation possibilities.
Use case 2
In the healthcare sector, wearable devices proud of their IoT crest monitor human health analytics, offering a protective cocoon around the sea of human life.
Use case 3
With industrial setups, IoT gracefully dances with machinery, enabling monitoring of product quality, tracking physical assets, predicting maintenance through ring-fencing, preventive manoeuvres, aided by ML-based algorithms.
ERP
A mainstay in the business technology lexicon for approximately 60 years, ERP has roots in Material Requirements Planning (MRP) systems of the 1960s. Today, these systems are vast reserves brimming with valuable data, essential for business operation. From material tracking to production planning, an ERP solution is critical for the successful management and integration of business functions.
ERP Top Features
- AI and Machine Learning: ERP employs artificial intelligence to streamline manual tasks and predict forthcoming business trends, contributing to a more efficient workflow.
- Internet of Things (IoT): Connected IoT devices provide a rich source of information for ERP systems, from tracking systems and sensors to cameras and scanners.
- Web-based Access: Today’s ERP solutions are accessible remotely thanks to web-based application design, increasing operational flexibility and effectiveness.
Top Features | Details |
---|---|
Data Granularity | With the reduction of data storage costs by cloud, ERP software can now collect highly detailed data for analysis. |
Security | ERP ensures data security, reinforcing trust in business operations while promoting efficiency in workflows. |
Global Team Connection | ERP promotes global connectivity, allowing teams from various locations to collaborate in real-time. |
ERP Limitations
- Implementation: A poorly executed ERP system implementation can lead to inefficiency or even hamper operations.
- Resource Intense: ERP solutions historically required a team of experts and significant resources to be developed, making them mainly accessible for large companies with sufficient budgets.
- Complexity: ERP can be relatively complex, making user adaptation potentially difficult. This is especially true for smaller businesses.
ERP Use Cases
Manufacturing
ERP’s origins in manufacturing make it an ideal tool for streamlining the management and oversight of inventory and production, particularly in large-scale operations.
Retail
For retail businesses, ERP offers a unified view of important business data from sales to inventory, enhancing decision-making and efficiency.
Service Industry
ERP can bring significant operation enhancement to the service sector through its ability to connect teams globally and provide greater visibility of real-time data.
MES
Behold, the essence of manufacturing excellence: Manufacturing Execution Systems or MES. A beacon of order in the whirlwind of manufacturing, it meticulously tracks the journey of raw materials as they transform into finished products in real time. Its benevolent gaze over inputs, personnel, machines, and support services empowers firms to make informed, timely decisions and scale up production.
MES Finest Features
- Product Lifecycle Management: Oversee a product’s journey from inception to disposal.
- Resource Scheduling: Assign resources where they are most needed, when they are most needed.
- Production Analysis: Unravel the story behind your manufacturing data.
- Downtime Management: Minimize disruptions to your manufacturing processes.
- Product Quality: Maintain the high standards your customers have come to expect.
- Materials Tracking: Stay in control of your resources throughout the manufacturing process.
Feature | Description |
“As-built” Record Capture | A historical logbook, it meticulously records data, processes, and outcomes – testament to MES’s astuteness in regulated industries. |
MES Limitations
- The cost of implementing MES can be considerable, ranging from $375,000 to $1.2 million.
- Creating a custom-built MES for complex manufacturing processes demands technological proficiency to ensure advanced data protection and seamless integration with existing IT systems.
MES Pricing
The price of harnessing the power of MES ranges significantly, from $375,000 to a staggering $1.2 million, depending on the unique needs of each manufacturing giant who dares to tighten the reins on their manufacturing units.
MES Use Cases
Use case 1: Regulatory Compliance
MES flourishes brilliantly in the reign of regulatory compliance. By tracking processes and outcomes, MES provides exhaustive “as-built” records – invaluable in regulated industries such as food, beverage, and pharmaceuticals.
Use case 2: Production Optimization
Firms craving optimization can leverage MES’s ability to reduce waste and setup times. It captures accurate cost information reflecting labor, scrap, downtime, and tooling, leading to production process refinement.
Use case 3: Automation
MES is a paragon of industry automation, adroitly managing workflows, scheduling, and equipment assignment. It rapidly identifies production bottlenecks, triggering alerts, and swiftly updates process plans in real time.
OPC: Boldly Bridging The Gap of Communication
Meet the OPC, born from an industrial automation task force in 1996, evolving beyond the traditional OLE to pave the way for unfettered data communication between control devices from varying manufacturers. It’s all about achieving real-time data exchange and breaking down the barriers of proprietary systems.
OPC: Pathbreaking Features
- Flinch-free Real-time Data Exchange: OPC DA ensures smooth and swift reading and writing of real-time control system data.
- Gold Mine of Historical Data: OPC HDA opens doors to a treasure trove of archived data, facilitating process improvement through historic insights.
- Be In the Know, Always: OPC Alarms and Events system guarantees you don’t miss essential alarm and event messages.
- Augmented Security: OPC UA comes stacked with comprehensive security measures, including end-to-end encryption, authentication, and auditing.
- Unparalleled Scalability and Flexibility: Consider every device as an independent object – hello enhanced scalability and flexibility!
Feature | Benefit |
---|---|
OPC Xi support for .NET Framework | Broadens Platform Support |
Collaboration with MTConnect Institute | Expands Industry Reach |
OPC-UA Integration | Supports wider platform range, from embedded microcontrollers to cloud infrastructure |
OPC: The Challenges
- Exclusive Access: Some OPC specifications are available only to OPC Foundation members. Need certification? Get trained first!
- Innate Dependence: OPC Servers utilize Microsoft’s OLE technology (COM) for real-time data exchange, implying the software’s reliance on Microsoft’s offerings.
OPC Usage Scenarios
Use Case 1: Plant Floor Device Data Accessibility
Seeking easy access to field data from plant floor devices? OPC servers play hero here, feeding disparate software packages with requisite data from a control device like a PLC or DCS.
Use Case 2: Secure Data Exchange in Industrial Automation
Chasing secure and reliable data communication in your automation space? You’ve found your match in OPC. Its interoperability standard ensures secure data exchange, through protocols like OPC DA that extract data from control systems, transferring the same to other systems on-site.
Use Case 3: Unifying Data Across MES and ERP
In a world dominated by XML and Web services, OPC UA holds its ground, combining existing OPC interfaces, XML, and additional tech to support MES and ERP systems. It champions platform independence, thanks to Java, Microsoft .NET, or C implementation possibilities.
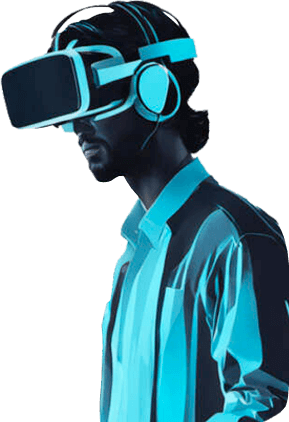