How will Augmented Reality bridge the generational gap in industry?
There was a short story being shared around LinkedIn about a ship with engines that would not start. This is going to be paraphrased a bit, but this retelling is in keeping with the spirit of the original.
Storytime…
The owners of a large seafaring vessel had an engine that would not start, with no indication of why. They hired all manner of consultants to evaluate the engine, the systems leading to it, and none could figure it out. So the ship sat idle, costing a fortune.
One day, a wizened engineer happening by the dock offered to take a look at it. Desperate, they told him to go for it. Taking a small hammer into the engine bay, he spent some time walking around, tapping on various parts of the engine, asking them to turn it over so he could listen.
After a couple of hours the engineer stops and takes out his hammer, and strikes a part of the engine with it a few times. He tells the owners to start the engines. They were skeptical, until the engine suddenly rumbled to life.
They looked at this man holding his hammer, absolutely bewildered. They ask “how much would you like to be paid for this?”
The man pauses and says: “$20,000”
Their bewilderment turned to shock as they could not believe what he had just asked for!
“$20,000!!! That only took a couple of hours! I will need an itemized invoice explaining why you think $20k is justified!”
“Sure, got a pen and some paper?”
They hand it to the man, who then proceeds to quickly scratch out an invoice.
This is what it read:
Engine Repair…
Hammer: $2
Knowing where to use it: $19,998
That to me is an example of the value in expertise and knowledge that can only be gained by years of working in a profession. What happens if that engineer had never walked by? Or more to the point, what if that engineer decided to retire, or go to work at another port?
How do we keep the engines humming when those who helped build them are no longer around to swing their hammers?
Looking at the problem today, we take notes from the past…
When one looks at apprenticeships of old, it was critical to bring the future leaders of any industry into the fold when they were young. It took many years to transfer all of the experience and skills of those that had mastered a trade, into the minds and hands of those that would follow in their footsteps.
For a time, people started out too young, but now we have labor laws to keep that in check. However, somewhere between children working in a coal mine, and a 22 year-old engineering graduate, there was a lapse in efforts to keep these bridges to the past from collapsing.
Now we see a significant gap between those that know things, down deep in their bones, to those that only know what they have seen in textbooks. This article from Inc.com discusses this gap and how to bridge it using traditional methods, independent of industry, but it fails to latch onto the distinct needs of the process industry.
This is not a new problem…
New engineers in plants are often relegated to shadowing those with more experience, given work to keep them busy, or tasked with escorting vendors into the plant. Just look at articles like this, where they give guidance for how new engineers can “rock” their new jobs. There are a lot of asking questions and trying to find work, and building confidence over time.
Now this varies depending on the organization, but ultimately they are limited in what they can do because those that are tasked with teaching them are still busy performing the same job in the first place.
Learning and reaching a level of proficiency often takes years, and exposure to many different operating conditions.
This is costly, and is never going to effectively capture the expertise of the outgoing generation. How can this way of operating be changed to meet the demands of these industries?
Augmented Reality will be that bridge, that data link to the ever elusive “tribal knowledge”
Under the current mode of operating, knowledge is generally passed from individual to individual. While this is beneficial, there is little in the way of widespread access across the organization. The ability to then translate this knowledge into real-world context is limited. After all, a new maintenance engineer is not going to understand that compressor COMP-101 is not performing as it should when he walks by and listens to it.
(Yes, his left knee also hurts when rain is coming.)
Thinking about the tools and technology
Advanced analytics layered onto critical assets in the field, with context displayed in front of an engineer on a pair of augmented reality glasses will provide the same diagnostic knowledge. More critically, it will be able to link this engineer to expertise stored in the cloud that can guide them through the evaluation and resolution of issues that have an impact on operations.
No longer are operations and maintenance managed from screens in a room or dusty manuals in a cabinet. Now everything is accessible, quite literally placed in front of their eyes.
A complete shift in operational mindset
Now the engineer that has been on the job for 6 months is no longer sitting through online training. Instead they can leave the office and be guided to the process area, shown operational information as they stand right in front of the unit. They can see the impact of these changes on the performance of the process and the individual components that make up the process.
The more experienced engineer can add their knowledge of various process and asset conditions to the system, allowing it to be accessible by all.
Imagine all of this working in concert with other digital transformation efforts, making the move from siloed units of information to an integrated and adaptive plant environment. These advancements in the realm of cloud-computing, data-driven machine learning and advanced analytics are already happening. Augmented reality is what will bring that data into the real world, and make it usable.
This article from Efficient Plant, written back in 2018, is just one of many over the last several years that have been highlighting the efficiencies gained by implementing augmented reality.
Ships and Hammers
Thinking back to our ship’s broken engine at the start, always remember one thing. Augmented reality can show an engineer how to swing the hammer, where it needs to land and even how hard it must be swung…
But only the engineer can pick up the hammer and make it happen.
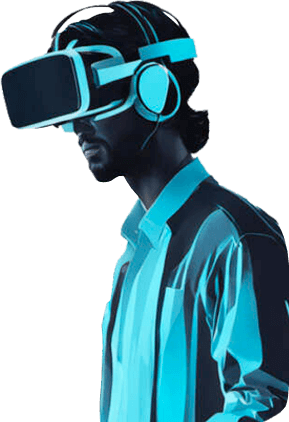