11 Worthy IoT Alternatives in 2024
IoT refers to a network of devices with embedded sensors and software exchanging data over the internet. Various technologies such as low-cost sensors, cloud computing, and AI play a crucial role in IoT practicality. Adopted across multiple industries, IoT devices vary in size and function, enabling improved efficiency and safety in various sectors.
For those exploring alternatives to IoT, potential options encompass MQTT, OPC, SCADA, DCS, PLC, ICS, MES, BAS, DAS, RTU, ERP, and more.
MQTT
Originally developed for low-bandwidth, high latency networks, MQTT (Message Queuing Telemetry Transport) has become a stellar player in IoT and IIoT applications, thanks to the rise of digital services, mobile capabilities, and edge computing.
MQTT Top Features
- Highly scalable, designed to accommodate millions of connections with low-power devices on low-bandwidth networks.
- Enables reliable and efficient machine-to-machine communication through the TCP/IP foundation.
- Offers secure data transaction through modern authentication protocols such as OAuth, TLS1.3, and Customer Managed Certificates.
- Additional specification, Sparkplug, enhances MQTT’s prowess in mission-critical applications, offering a standard topic namespace, enhanced state management, and rich payload data.
- Compatible with several programming languages including Python for easy implementation.
Feature | Description |
---|---|
Publish-subscribe architecture | Decouples data-producing devices from data-consuming applications, optimizing network performance. |
Support for password and token authentication | Boosts security, required for IoT systems. |
Integration with AWS IoT Core | Facilitates connectivity with billions of IoT devices, routing trillions of messages to AWS services. |
MQTT Limitations
- Lacks native support for data integrity checks, requiring external validation methods.
- Relies heavily on the quality of the implementation and the network stability.
MQTT Use Cases
Use case 1: Hydraulic Fracturing Operations
With MQTT, remote data collection in hydraulic fracturing operations becomes a breeze, increasing efficiency and reducing associated risks.
Use case 2: Distributed Multisite SCADA
MQTT enhances cross-site data integration in SCADA, optimizing the management of distributed sites.
Use case 3: IoT and IIoT applications
As a powerful protocol for the Internet of Things (IoT) and the Industrial Internet of Things (IIoT), MQTT contributes to the connectivity of diverse devices, fostering the global tech unity across regions and cultures.
OPC
Emerging from the vaults of technological lore in 1996, Open Platform Communications (OPC) has evolved into a paragon of industrial telecommunication, enabling harmonic data communication between varied control devices.
OPC Top Features
- Interoperability: OPC’s open standard facilitates extended compatibility, ensuring reliable data exchange between control devices from disparate manufacturers.
- Extensive Application: Broadening its horizons, OPC technology now holds its sway in diverse areas like building automation, process control, discrete manufacturing, and more.
- Platform Independent: OPC UA’s design endorses platform independence, thus can be implemented with robust platforms like Java, Microsoft .NET or C.
- Comprehensive Security Measures: OPC arbitrates end-to-end encryption, robust authentication, and stringent auditing, fortifying system security to a remarkable extent.
- Scalability: Each device within the OPC model is viewed as an independent object, enhancing scalability and flexibility.
Features | Description |
---|---|
OPC DA | Facilitates real-time data reading and writing. |
OPC HDA | Allows access to archived data. |
OPC Alarms and Events | Promotes exchange of alarm and event messages. |
OPC Limitations
- Standard Access: Certain OPC specifications are only accessible to OPC Foundation members.
- Complex Implementation: For beginners or those unfamiliar with Microsoft’s OLE, COM, and DCOM technologies, establishing OPC servers can be complex.
OPC Use Cases
Use Case 1: Industrial Automation
OPC plays a vital role in facilitating smooth data exchange, thereby improving operational efficiency and productivity in industrial automation scenarios.
Use Case 2: Building Automation
In the sphere of building automation, OPC renders simplified controls integration, asserting enhanced building performance and energy management.
Use Case 3: Process Control
With its comprehensive security measures, effortless data exchange, and welcoming flexibility, OPC ensures continuous process improvements on the manufacturing floor.
ERP
An ERP (Enterprise Resource Planning) system is the lifeblood of businesses across the globe, integrating functions, improving processes and paving the future with AI and IoT.
ERP Top Features
- Integrates all processes needed to run a company.
- Improves reporting, efficiency, accuracy, and productivity.
- Increases collaboration with web-based applications for remote access.
- Leverages AI and machine learning, eliminating manual tasks and predicting business trends.
- Exploits IoT devices for an influx of information.
Feature | Benefit |
---|---|
Data Security | Guards critical business data |
Efficient workflows | Promotes streamlined operations |
Real-time data | Enables informed decision-making |
ERP Downsides
- Unsuccessful implementation can lead to inefficiency or ineffective operations.
- Requires a significant investment of time and resources.
ERP Pricing
Pricing varies among vendors like Oracle, Microsoft, SAP and newer contenders as Bizowie and Workwise. Some offer cloud-based solutions that can reduce costs associated with hardware purchases and maintenance.
ERP Use Cases
Use Case 1: Large Enterprises
An ERP system is particularly beneficial for large businesses with vast operations to manage and resources to invest.
Use Case 2: Manufacturing Firms
Historically, manufacturing firms like J.I. Case have used ERP systems to track inventory and production scheduling.
Use Case 3: Small-Medium Businesses
With the advent of cloud ERP, even small-medium businesses can access effective systems without large upfront hardware costs.
SCADA
Unveiling SCADA, the powerhouse of Supervisory Control and Data Acquisition which is a centralized system adept at monitoring and controlling an entire network. Primarily deployed in industries like energy, transportation, and telecom, SCADA automates complex industrial processes, offering solutions even before problems surface.
SCADA Top Features
- Efficient Monitoring and Control: SCADA facilitates site control using field devices like RTUs or PLCs. RTUs enable efficient and secure monitoring while PLCs might entail a higher cost in the long haul.
- Comprehensive Components: Comprising of hardware like sensors, communication channels, control relays, SCADA master units, input/output signal hardware, and the Human-Machine Interface (HMI).
- Flexible Communications: SCADA supports communication over Ethernet and IP over SONET, further facilitated by NetGuardian 832A for a gradual shift to IP capable devices.
- Evolution Over Time: SCADA systems evolved from being monolithic to distributed and networked systems, now incorporating SQL databases and rapid application development (RAD) capabilities.
Future Directions | Benefits |
---|---|
5G networks & Quantum Computing | Increased Connectivity & Speed |
Edge Computing & AI | Advanced Decision Making & Analytics |
SCADA Limitations
- Cybersecurity Concerns: With increasing connectivity, SCADA systems are more prone to cyber threats.
- Legacy Constraints: Older SCADA systems lack scalability, interoperability, and accessibility to data and controls, with limited options for support.
SCADA Use Cases
Use case 1
Owing to its real-time monitoring capabilities and in-depth data logging, SCADA proves advantageous for the energy sector in managing power distribution and outages.
Use case 2
Manufacturing industries leverage SCADA systems for automated process control, leading to decreased downtime and improved productivity.
Use case 3
In the transportation industry, SCADA systems aid in monitoring and controlling traffic signal control, incident detection, and dynamic message signs.
DCS: Distributed Control System
Stepping onto the transformative stage of automation and control, we introduce DCS – a titan of distributed functionality, epitomizing the interdisciplinary magic of integration, set against an empirical backdrop of a projected $23.37 billion revenue by 2025.
DCS Top Features
- Decentralized Control Principle: DCS offers individual monitoring and control of process plant components.
- Structural Design: Incorporates an engineering workstation, operating station, process control unit, communication system, and smart devices.
- Flexibility: Seamless integration to existing industry architecture. Supports modifications & upgrades.
DCS Feature | Benefit |
---|---|
Centralized Operator Supervisory Control | Enhances reliability and reduces installation costs. |
Mitigation against Single Processor Failure | Insulates against detrimental effects of system failure. |
Database Management | Robust set of configuration tools for control logic, graphics, and system security. |
DCS Limitations
- May not be ideal for real-time actions, that’s where PLC (Programmable Logic Controller) shines.
- More suited for larger facilities dealing with substantial I/O points, complex and large plant environments.
DCS Use Cases
Power Generation
DCS finds powerful application in the power generation sector, handling complex processing and control tasks with tantalizing precision.
Oil and Gas Industry
Within the slippery contours of the oil and gas industry, DCS proves pivotal in optimizing interactions among numerous controllers, enhancing safety and production efficiency.
Manufacturing
DCS casts a manufacturing marvel, easing maintenance throughout plant life cycle while escalating production efficiency.
PLC – The Power Behind Automation
Originating in the dynamic era of the 1960s, the Programmable Logic Controllers (PLCs) have evolved to become vital lifelines in the infrastructure of the manufacturing industry. The journey from suitcase-sized entities to conveniently small, powerful units epitomizes the technological advancements.
PLC Top Features
- Bonafide standardization accomplished by the IEC 61131-3 Standard, optimizing understanding and use of the programming language.
- Revolutionary integration with ERP, MES systems and SCADA contributes to efficiency and performance in manufacturing operations.
- Advanced capabilities and core functions aided by cutting-edge processor, memory technology enhancements.
- PLC maintains the ability to monitor and record enigmatic run-time data such as machine productivity, operating temperature – a boon for start-stop processes and alarming during machine malfunctioning.
Vision System Integration | Deepens consumer-friendly interaction |
Motion Control | Enables precise device operation |
Multiple communication protocols | Ensures synchronized support |
PLC Limitations
- Troubleshooting can often pose significant challenges.
- Demands a well-trained, skillful workforce.
PLC Use Cases
Use Case 1: Innovative Technologies
Distinctively favorable in industries requiring expensive data acquisition systems due to decreasing cost, size of solid-state memory.
Use Case 2: Advanced Manufacturing
Profoundly beneficial for industries like automotive, airport control systems, where robust control, monitoring are critical.
Use Case 3: Intellectual Property
Essentially crucial for systems requiring high-quality control mechanisms.
ICS
Industrial Control Systems (ICS) represent the innovative fusion of devices, systems, and controls that drive the heart of industrial processes. With their extensive capabilities, ICS hold potential to revolutionize industry operations and automation.
ICS Best Features
- IT & Operational Technology (OT) integration: Greater cohesion between IT and OT variables leads to amplified supply chain visibility.
- Distributed Control Systems (DCS): Optimization of production control within a single location via a centralized supervisory control loop.
- SCADA Server: Effective for long-distance process monitoring and control, elevating supervisory level control. A core of devices like PLCs facilitates efficient distribution across various sites.
- Communication protocols: Adoption of widely utilized communication protocols (Process Field Bus (PROFIBUS), Distributed Network Protocol (DNP3), Modbus, Open Platform Communication (OPC)) ensures flexibility and compatibility.
Feature | Benefit |
---|---|
Control Loop | Maintains operating conditions within specific limits, enhancing process stability and reliability. |
Data Historian | Archives and retrieves historical operational data, contributing to efficient troubleshooting and enhanced decision-making. |
Human Machine Interface (HMI) | Improves ease-of-use, reducing operational errors and increasing process efficiency. |
ICS Limitations
- IT/OT convergence: While promising improved integration and visibility, this convergence also presents larger attack vectors for cybercriminals.
- Vulnerability to targeted cyberattacks: The digitization of ICS increases exposure to new threats. The escalated danger follows the advent of cloud computing, big data analytics, IoT, and other emergent technologies.
ICS Use Cases
Manufacturing
ICS excel at enhancing production efficiency, reducing the impact of faults and spurring significant improvements in manufacturing output. Deploying DCS, for instance, manufacturers can ensure smooth operations with minimal disruptions.
Transportation
ICS brings improved visibility and control over complex transport networks. Leveraging SCADA technology, operators can monitor and control expansive transportation infrastructure from a central hub.
Energy
ICS technology is crucial in ensuring stability and efficiency in intricate power generation systems. With the aid of Data Historian functionality, energy suppliers can identify trends, optimize generation processes, and anticipate potential operational issues.
MES
At the intersection of manufacturing and technology, resides MES or Manufacturing Execution Systems. These systems embody the ultimate marriage of real-time data and decision-making, presenting a hub for all elements, spanning inputs, outputs, personnel, machines and support services. Regulated industries, such as food and beverages or pharmaceuticals, benefit greatly from as-built records proffered by MES.
MES Top Features
- Product lifecycle management: MES provides oversight throughout the entirety of a product’s life cycle.
- Resource scheduling and order execution: This functionality ensures maximized efficiency and optimized production output.
- Production analysis and downtime management: MES can identify production hiccups and remedy them in real-time.
- Quality control: The ability to monitor and ensure the consistent quality of products.
- Materials tracking: MES facilitates tracking from raw materials to finished goods with adept precision.
Feature | Description |
---|---|
Planning of resources | Ensures help is allocated where and when it’s most needed. |
Monitoring production | Real-time tracking of production activities for enhanced decision-making. |
Process Automation | Automated workflows and alerts for product bottlenecks. |
MES Limitations
- High initial cost: The cost of implementing MES could be a limiting factor for some, with ranges from $375,000 to $1.2 million.
- Complexity: Custom-built MES solutions cater to complex manufacturing processes which may be intricate to navigate.
MES Pricing
The cost of implementing MES can vary greatly; typically, initial costs range from $375,000 to $1.2 million.
MES Use Cases
Use Case 1: Regulated Industries (e.g., Food, Beverage, Pharmaceuticals)
For businesses in industries such as food, beverage or pharmaceuticals, MES can ensure regulatory compliance by providing an ‘as-built’ record, capturing data, processes, and outcomes.
Use Case 2: Businesses Seeking Operational Efficiency
MES aids in upscaling production output through real-time monitoring and decision-making, thus optimizing operational efficiency. These systems also reduce waste and inventory, while increasing uptime.
Use Case 3: High Output Manufacturing Businesses
With its ability to manage product genealogy and detect potential issues, MES is invaluable for businesses focusing on high output. It helps streamline the production process while maintaining high-quality standards.
BAS
Arising from the innovative mind of Dutch Cornelius Drebbel in the 1600s, Building Automation Systems (BAS) have evolved immensely, paving the way for a revolution in control systems. BAS transforms traditional buildings into smart ones, managing everything from heating, ventilation, and AC to lighting systems. Imagine a future where your buildings are scalable, energy-smart, and capable of impressive feats–that’s the power of BAS!
Top Features of BAS
- Enhanced Interoperability: Owing to the BACnet protocol, BAS can enjoy easy integration across different systems.
- Energy Conservation: Modern BAS are now an integral part of green buildings designed to save energy, water, and air.
- Integration with systems: Modern BAS can seamlessly link with security, lighting, and even elevator control systems.
Feature | Description |
---|---|
Scalable | BAS systems are designed to grow with your needs, ensuring longevity and versatility. |
High Revenue Generation | BAS has a flourishing market, expected to reach an estimated $100.6 billion by 2022! |
BAS Disadvantages
- Improper Configuration: If not correctly implemented, BAS can account for significant energy usage.
- Dependence on Protocols: While BACnet has improved interoperability, the success of a BAS hinges on the chosen protocols.
BAS Use Cases
Lighting
With the right BAS, lights can switch on based on room occupancy, drastically optimizing energy usage.
Security
BAS can be integrated with access control and other security systems, enhancing building safety.
Energy Management
BAS are instrumental in reducing energy usage and maintaining climate within specified parameters, making buildings greener and more sustainable.
DAS
In the high-tech dance of wireless connection, the DAS (Distributed Antenna System) swoops in as an elegant ballerina, addressing the common challenge of poor in-building coverage. Through a dense network of petite antennas, functioning much like lyrical repeaters, they connect to a central controller that diligently choreographs the dance with wireless carrier network’s base station. This virtual waltz is as seamless to the mobile devices as the moonlight on a clear night, offering voice and data services akin to any cellular network tower.
DAS Top Features
- Deploys a delicate dance of small antennas as magical repeaters, eliminating poor in-building coverage.
- Streams signals from roof antennas through ether-like fiber cables, with active systems amplifying signals as needed.
- Offers a chameleon-like transparency to mobile devices, shadowing any cellular network tower’s voice and data services.
- Universally compatible. Wear it like a versatile black dress, it interfaces any experiment to computer for data recording/processing with the capacity to handle up to 240 analog or digital outputs.
- Incorporates a blooming network of automation via AIMOS, making management as easy as a summer breeze. It accommodates fault analysis for troubleshooting, auto-executes tasks, and fits seamlessly into third-party network management software.
Modular Capacity | Address Bus Capacity |
---|---|
Up to 240 analog or digital outputs | 8 bits address bus with 16 addresses for internal use and up to 240 distinct analog or digital inputs |
Transmission Speed | Baud rate ranges between 150 to 38.4 kbaud, with a special 32k bps allocation for NASA serial data standard |
DAS Disadvantages
- The song of DAS comes with an unfortunate refrain – labor-intense installation processes that make deployments costly.
- Travel distance, building characteristics, and technical demands influence DAS installation costs, akin to the way an artist’s palette affects the final masterpiece.
DAS Pricing
While DAS, like a grand symphony, thrills with its performance, it draws a hefty ticket price due to labor-intense installation processes. The exact monetary duet is composed of various factors such as travel distance, building characteristics, and technical demands. A more accurate aria of costs can only be conducted after comprehensive site surveys and RF benchmarking tests.
DAS Use Cases
Use Case 1: High-rise Buildings
Like a lighthouse on a cliff, DAS bathes towering skyscrapers in a luminous pool of connectivity, banishing the shadow of poor reception. Its modular design sings a harmony with the architecture, ensuring every nook and corner is awash with impeccable signal strength.
Use Case 2: Malls
In the bustling opera of shopping malls, DAS emerges as a medley of connectivity, ensuring the rhythm of purchase and enjoyment never skips a beat.
Use Case 3: Medical Centers
Breathing life into hubs of healing, DAS fits seamlessly into medical centers, ensuring the lifeline of communication blossoms across wards and units, as essential as the heartbeat it supports.
RTU
The RTU (Remote Terminal Unit) is a microprocessor device that forms an interface between real-world objects and control systems like SCADA. With a design to withstand harsh conditions, it can work in extreme environments and is widely used for remote monitoring across different industries.
RTU Top Features
- Operates under extreme conditions
- Supports IEC 61131-3 programming standard
- Communicates via RS485 or wireless links
- Monitor different types of analog inputs
- Modifies behavior in response to physical override switches in autonomous mode
Feature | Description |
---|---|
Acquisition of Real-World Info | Acquires real-world info from isolated voltage or current sources. |
Data Transmission | Sends telemetry data to master system and receives control messages. |
Power Efficiency | Typically power efficient and often uses solar power. |
RTU Limitations
- Differentiated by input and output capacities
- Potentially high current capacity required to switch power to field devices
- Requires setup software for data streams and communication protocols
RTU Pricing
RTUs come in varied price points, from entry-level priced at around $500 to premium variants which can cost over $5,000. Higher-end RTUs, with their enhanced features and capacities, command a premium price.
RTU Use Cases
Use case 1 – Industrial Applications
RTU is used for remote monitoring in industries like oil and gas, electric, water utilities, and automobile manufacturing. Given its robust design, it can operate in extreme industrial conditions.
Use case 2 – Environmental Applications
RTU plays a vital role in environmental projects like the Biosphere 2 as it can function in hard-to-reach locations.
Use case 3 – Food Processing
In the food processing industry, RTUs monitor and control critical parameters like temperature, ensuring product safety, and quality.
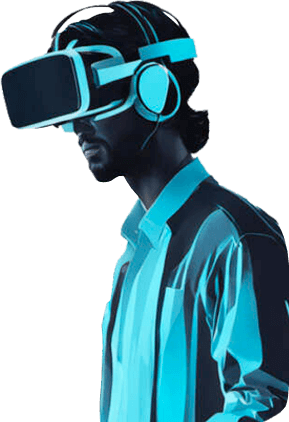