Top 15 Picks for PLC Alternatives in 2024
SCADA
SCADA, abbreviated from Supervisory Control and Data Acquisition, is an ingenious computer application designed to control and monitor plant or equipment at a supervisory level. It’s an integral part of many industries including energy, water control, oil and gas refining, transportation, telecom, and more. It carries out complex automation of industrial processes, detects and corrects problems efficiently, and records data to track trends over time.
SCADA Top Features
- Centralized Control: SCADA provides a comprehensive network monitor and control system. This results in powerful and efficient supervision of large-scale processes.
- Advanced Components: The SCADA system consolidates various components like Remote Terminal Unit (RTU), sensors, control relays, SCADA master units, and communication channels. Additionally, it incorporates a Human-Machine Interface (HMI) and software capabilities.
- Diverse Sensors: SCADA employs both discrete and analog sensors. Discrete ones collect digital info from equipment while analog sensors measure live values from environmental conditions.
- Upgraded Communications: Data transmission is achieved via Ethernet or IP over SONET. With the support of NetGuardian 832A, gradual migration over time to IP capable devices at remote sites is possible.
- Future-Directed Technology: The system is set to integrate 5G networks and quantum computing for enhanced operational capabilities. Contemporary SCADA systems also explore the potential of edge computing, AI, and machine learning as the next big steps.
Components | Functions |
---|---|
SCADA Field Devices | Monitor and control sites, often serving as efficient alternatives to PLCs. |
Human Machine Interface (HMI) | Acts as a master station, processing data and communicating it to human operators. |
SQL Databases & RAD Capabilities | Used in modern SCADA for storing, retrieving, and quickly developing applications. |
SCADA Limitations
- Cybersecurity Concerns: With more integrated and connected systems, SCADA grapples with digital security issues.
- Lack of Scalability: Legacy SCADA systems have limited support and lack interoperability, thereby limiting system upgrades and expansion.
- PLC Costs: Using Programmable Logic Controllers (PLCs) within the SCADA system can often result in long-run costs.
SCADA Use Cases
Use case 1: Industrial Plants
SCADA shines in industrial plants where it optimizes complex process automations. Accessibility to real-time data allows operators to rectify problems promptly, ensuring smooth and efficient workflow.
Use case 2: Transportation
Within the transportation sector, SCADA controls and monitors systems remotely. This aids in managing large-scale operations effectively and mitigating potential issues promptly.
Use case 3: Oil and Gas Refining
SCADA has a prominent role in the Oil and Gas industry where the real-time data logging and immediate problem detection prevent costly breakdowns and maintain consistency in production.
DCS: Distributed Control System
Allow the flow of your attention to be captured by the thrill and innovation of the DCS: the Distributed Control System. A beautifully automated control framework, spreading functionality far and wide across countless elements, with a global presence anticipated to burgeon to an impressive $23.37 billion by 2025. Its usage, as fluid and versatile as the industries it adorns, it masters and controls processes with the grace and precision only matched by the most skilled artisan.
DCS Top Features
- DCS offers the cardinal ability to manage and control processes; a gift pivotal in processing management across industries.
- It is the thread that weaves together individual control, reporting, and monitoring components in process plants.
- Deep inside DCS’s heart stay set configuration tools dedicated to database management, control logic, graphics, and system security.
- Further, this system supports modifications, upgrades, and elegant integration into extant industry architecture.
Centralized operator supervisory control | Enhances reliability while minimizing installation costs |
Mitigates single processor failure effects | Structured to withstand the storm of technological hiccups |
Integrated common command structure | Promotes seamless and efficient information distribution |
DCS Downsides
DCS VS PLC | Benefit |
---|---|
Real-time controller effectiveness | PLC tends to outshine DCS in swift real-time actions |
Scale and Complexity | DCS can be overkill for smaller facilities or less complex processes that PLC could handle adequately |
DCS Use Cases
Power Generation
DCS has proven to be a beacon of operational prowess within the power generation industry; precise control coupled with broad platform integration makes it an exquisite choice.
Oil and Gas Industry
Imbued with the turbo-charged capacity to handle substantial I/O points, DCS shines within the oil and gas industry, easing intricate and large-scale control.
Biotech and Pharmaceuticals
Revolutionizing the world of pharmaceuticals and biotech, DCS fosters enhanced production efficiency and safety measures. It truly streamlines maintenance throughout the plant lifecycle.
IoT
Internet of Things, or IoT, ushers you into a world where your devices don’t just exchange pleasantries, but meaningful data – a world where your car could book its own spa appointment or your fridge might judge you for your late-night cheeseburger cravings. With sensors, software, and everything in between, IoT is the glue that holds our increasingly connected lives together.
IoT Top Features
- Connectivity: With IoT, your devices can mingle on the internet and be part of the global town square.
- Machine Learning: When your IoT device is taking a coffee break, machine learning steps in to pick up the slack, analyzing data and making sense of patterns.
- Microcontrollers: Microcontrollers are like the tiny brains inside IoT devices, making crucial decisions about data transmission and control.
- Data-Driven Insights: IoT plays Sherlock, generating insightful data to drive efficiency and potentially unleash new business models.
- New Revenue Streams: IoT’s ingress into diverse sectors hints at its potential to set up new revenue streams, diversifying income portfolios.
Feature | Benefit |
---|---|
Automation | All the work, less the hassle. IoT enables automation for industry sectors, making daily operations smoother and more efficient. |
IoT Control Center | A central control command to manage IoT devices across the globe. It’s like being a tech superhero without the fancy costume. |
Smart Manufacturing | Imagine your factory with a brain of its own. Thanks to IoT, smart manufacturing is making that wild thought real. |
IoT Limitations
- No matter how smart, your IoT device is a house of cards without a good internet connection.
- IoT’s intelligence is only as good as the data it receives. Garbage in, garbage out!
- Despite IoT’s incredible utility, it can sometimes be too complex for users without a good degree of tech-savviness.
Use Cases
Automotive Industry
IoT goes vroom vroom alongside your car, enabling manufacturers to maintain a continuous relationship with customers. Your car could get new software upgrades or even book its own service appointments. How’s that for private chauffeuring?
Retail
Tired of inventory mistakes in retail? IoT to the rescue! With improved inventory management and customer insights, IoT plays a substantial role in taking your retail business to a whole new level.
Home Automation
Ever dreamt of living in a Jetsons-style future? IoT makes that possible with easy control of lighting, heating, and even security systems. Coming home to a preheated oven and cozy living room? Count us in!
BAS
Let’s turn back the dial to the 1600s, when Cornelius Drebbel—a Dutch innovator with a talent for HVAC—stoked the furnace of the world’s first building automation system (BAS). Today, BAS takes the lead in managing heating, lighting, security, ventilation, and even systems as futuristic as sterilization, all in an effort to create a climate-perfect, energy-efficient environment.
BAS Top Features
- Adopts BACnet protocol for enhanced interoperability
- Utilizes Niagara controls framework released by Tridium for integrating various protocols
- Leverages ABB’s Aspect system for efficient HVAC controls
- Integrates multiple controls including Trane, Carrier
- Designed to accommodate in most green buildings for effective energy, air, and water conservation
Feature | Benefit |
---|---|
Interoperability | Compatible with various protocols for seamless function |
Integration | Combines multiple controls for broad coverage |
Conservation | Promotes energy, air, and water conservation in green buildings |
BAS Downsides
- If improperly configured, BAS can contribute to roughly 8{66f7997927a862c9f57ec7dffc6a2fe6d405caee7001dff533b976d48fe118b1} of the total energy use in the USA
- In many traditional buildings, systems like heating, ventilation, AC, and lighting operate independently, limiting their functionality
BAS Use Cases
Use case 1: Green Buildings
Sprouting like celery sticks across the globe, green buildings are the perfect playgrounds for BAS. Its energy-conscious credentials slot into the ethos of green design: effective conservation, be it of energy, air, or water. And let’s face it, who wouldn’t want an automated environment!
Use case 2: New Constructions
If you’re adding another pillar to the North American skyline, hello BAS! North America is spearheading BAS implementations in new buildings. Fenestrations and basements get a high-tech friend to control temperatures and energy usage, bringing in some cool (perhaps literally) dollars!
Use case 3: Traditional Buildings
Creaky, old buildings groaning with isolated HVAC, lighting systems? Enter BAS. Marching towards a $100.6 billion market by 2022, BAS can stitch together these independent systems, pulling them into the 21st-century energy-conscious era.
DAS
Meet DAS (Distributed Antenna System), the audacious savior of poor in-building coverage. This maverick technology is a system of small antennas acting as repeaters; creating robust cellular networks inside buildings.
DAS Top Features
- Comprehensive coverage: DAS provides voice and data services similar to any cellular network tower, right inside your building.
- Versatility: This system is modular and interfaces with any experiment for data recording or processing.
- Multi-carrier support: DAS can be shared by multiple carriers, reducing the overall cost.
- High capacity: It handles up to 240 analog or digital outputs with a baud rate ranging from 150 to 38.4 kbaud.
- AIMOS: An automated and powerful DAS management platform, offering robust fault, configuration, and inventory management capabilities.
Features | Benefits |
---|---|
Active DAS | Amplifies signals ensuring continual strong network |
Passive DAS | Utilizes leaky feeder cables for an economical signal distribution solution |
Automatic operations on AIMOS | Automates tasks like alarm polling, RF frequency allocation, network element software updates |
DAS Limitations
- Installation cost: Labor-intensive installation processes make DAS deployments costly.
- Carrier dependency: Costs are usually borne by the carrier, demanding their involvement.
DAS Pricing
Specific pricing ranges are provided post-site survey and RF benchmarking owing to the influence of building characteristics, existing infrastructure, and technical needs on installation costs. Transparency in pricing is maintained.
DAS Use Cases
Use case 1: High-rise Buildings
In these concrete jungles where connectivity could be a nightmare, DAS ensures impressive in-building cellular network performance, right from basement to the penthouse.
Use case 2: Medical Centers
From patient data transmission to vital communication, DAS fortifies every corner with strong network coverage, making it critical for health-care edifices.
Use case 3: Shopping Malls
Imagine a mall where every selfie shared, every payment made, executes lightning fast. That’s the power of DAS.
RTU
Enter the versatile world of RTU (Remote Terminal Unit). An advanced microprocessor-controlled electronic device, RTU interfaces between real-world objects and SCADA (Supervisory Control And Data Acquisition) systems or distributed control systems.
RTU Top Features
- SCADA Integration: Transmits telemetry data to the master system, while also receiving control messages for linked interactions.
- Hardy Design: RTUs resist hostile conditions, making them perfect for pipeline and grid guarding systems, secluded locations, or severe environments, such as Biosphere 2 projects.
- Power Efficient: Typically, RTUs come with RS485 or wireless links, the power efficiency of which can be solar-powered.
Component Inclusion | RTUs incorporate essential components which include CPU, communication interfaces, input/output cards for digital input and output, analog input, and analog output. |
IEC 61131-3 Compliant | Modern RTUs follow the IEC 61131-3 programming standard suitable for programmable logic controllers. |
Real-time Data Interpretation | RTUs translate and scale raw data into relevant units during user communication through a human-machine interface. |
RTU Limitations
- Requires special configuration software to connect data inputs to data outputs, define communication protocols, and troubleshoot installation issues.
- May involve additional costs for high current capacity relays to switch power to field devices.
RTU Pricing
Clients enjoy a series of options with RTUs spread across different routines – entry-level, mid-range, and high-end – thereby making the price points flexible. The offerings start from a base price of $500, advancing to over $5,000 for premium models.
RTU Use Cases
Use Case 1: Industrial Automation
RTUs are integrated into the fabric of various industries like oil and gas, electric, water utilities, refineries, and food processing. Their ability to monitor analog inputs of different types in real-time gains significant importance.
Use Case 2: Automobile Manufacturing
In the automobile manufacturing sector, RTUs shine with their capability to drive high current capacity relays to switchboard, providing power to field devices.
Use Case 3: Remote Monitoring
RTUs aptly suit scenarios requiring remote monitoring, chiefly on account of their distinct design, which accommodates harshest conditions and ensures seamless communication.
MES
Manufacturing Execution Systems, MES, are computerized mechanisms levered in the manufacturing domain to streamline the journey of raw materials into final products. They adopt real-time data utilization to augment decision-making while intensifying production output.
MES Top Features
- Product Lifecycle Management: Efficiently supervises the complete lifecycle of the products.
- Resource Scheduling and Order Dispatch: Ensures optimal use of resources and timely order execution.
- Production Analysis and Downtime Management: Offers insights into production performance and minimizes downtime.
- Product Quality and Material Tracking: Ensures consistent product quality and real-time material tracking.
Feature | Benefits |
---|---|
Accurate Cost Information Capture | Reduces waste and setup times, while promoting uptime. |
Integration with ERP, PLC, etc. | Promotes process optimization and reduces waste. |
Automated Workflows | Facilitates employee scheduling, equipment assignment, and real-time updates. |
MES Limitations
- Deployment Cost: The implementation of MES can be expensive, ranging from $375,000 – $1.2 million.
- Complex Integration: Customizing MES solutions to align with existing IT systems can be complex.
MES Pricing
The cost of implementing an MES solution varies largely and can range from $375,000 to $1.2 million, contingent on the complexities and customizations required.
MES Use Cases
Use Case 1: Regulated Industries
MES is exceptionally beneficial for regulated industries, including food, beverage, and pharmaceuticals, offering real-time tracking of inventory levels, equipment and resource utilization, and maintenance history.
Use Case 2: Industrial Automation
MES solutions enhance the operational efficacy of industries employing automation by providing insights into potential issues leading to a significant reduction in downtime and maximization of production output.
Use Case 3: Complex Manufacturing Processes
Custom built MES solutions are extremely efficacious for industries with complex manufacturing work-flows. They provide advanced data protection and easy integration with existing IT architectures for optimal process optimization.
HMI: Bridging Humans and Machines
In a world where machines define progress, HMI (Human-Machine Interface) empowers us with interactivity! Not to be mistaken for the graphical interface we associate with our devices, HMI is the sophisticated connective tissue binding humans to machines, systems and industries.
Unveiling the Best of HMI Features
- Comprehensive Data Display – From time tracking production trends to monitoring machine inputs and outputs, HMI is your data-centric dashboard!
- Wide Industrial Applications – Energy, food, beverages, manufacturing, oil, gas, power, recycling, transportation, and water/wastewater sectors get an operational edge!
- Revolutionary Interaction – Funneling device inputs by touch, HMI gives operators, integrators, and engineers power-packed control.
- Highly Evolved Technology – HMI has quickly evolved over the past decade and now utilizing high-performance, touch screens, and mobile devices.
Benefit | Customer Impact |
---|---|
Mobile HMI | Allows operators instant remote monitoring and data access capabilities. Making critical decisions on the go has never been easier! |
HMI/SCADA Systems | Furnish industrial plants worldwide, enhancing visualization, situational awareness, and centralized control! |
Integration with Data Historian | Experience advanced historical trending and data analysis. |
Unearthing the Limitations of HMI
- Data acquisition primarily depends on PLCs (Programmable Logic Controllers) and input/output sensors.
- A radical mindset change can be required among employees to leverage full potential from HMI/SCADA systems along with cultural adaptation towards continuous improvement.
HMI Pricing
The journey towards digitizing and centralizing your data couldn’t get any better! While specific pricing isn’t mentioned, it’s all about ROI and the immense value that HMI brings to your operational horizon.
A Peek into HMI Use Cases
Use case 1: Oil and Gas Plants
With real-time operational visualization, alarm resolution and control over plant operations, HMI/SCADA fortifies decision making in oil and gas plants.
Use case 2: Water Treatment Facilities
From monitoring to alarming and control over operations, SCADA HMI is a game changer in water treatment facilities promoting efficiency at its best.
Use case 3: Power Generation Industries
HMI/SCADA systems in power generation industries ensure intelligent control, less time spent navigating systems, and faster identification of critical data for optimized operation.
Microcontroller
An integral component in embedded systems, a microcontroller is a compact integrated circuit which manages a specific operation. Withstanding various temperatures and ruggedied for tough conditions, these devices are often used in a myriad of applications – from vehicles to medical devices, and even in home appliances.
Microcontroller Top Features
- Compact Design: Contains a single chip housing a processor, memory, and I/O peripherals.
- Various Processors: Range from simple 4-bit, 8-bit or 16-bit processors to complex 32-bit or 64-bit processors.
- Memory Versatility: Includes both volatile (RAM) and non-volatile memory (flash memory, EPROM, EEPROM).
- Varying Architectures: Designed based on Harvard or von Neumann architecture for data exchange.
- Instruction Types: Can be based on complex instruction set computing (CISC) or reduced instruction set computing (RISC).
Programming Languages | C, Python, JavaScript |
Common Microcontrollers | Intel MCS-51, AVR by Atmel, PIC from Microchip Technology, ARM microcontrollers |
Manufacturers | NXP Semiconductors, Renesas Electronics, Silicon Labs, Texas Instruments |
Microcontroller Limitations
- Sophistication: Less sophisticated compared to Systems on a Chip (SoCs) and can have lesser digital controls.
- Program Memory: Limited choices, often contains Ferroelectric RAM, NOR flash or OTP ROM.
- Performance: More demanding roles may require more DSP-like functions, higher clock speeds, and a more robust memory.
Microcontroller Use Cases
Use case 1: Building Automation
With diverse types of I/O pins and low power consumption, microcontrollers are ideally suited for integrating various building automation systems together.
Use case 2: Robotics
Microcontrollers can handle specific operations in robots, making them capable of performing complex tasks with a high degree of precision and reliability.
Use case 3: Automotive
Due to their rugged design, ability to withstand various temperatures, and specific operation control, microcontrollers are increasingly being used in automotive applications.
Relay
Relay is an electrically operated switch that ingeniously controls different circuits via an independent low-power signal. Having made its mark since its operation in long-distance telegraph circuits, telephone exchanges, and early computers, Relay has evolved greatly and is now a cornerstone of many innovative systems.
Relay Top Features
- Cost-effectiveness: Relay proves its economic advantage when replacing three or more relays, presenting cost-saving implications in equipment, installation, troubleshooting, and labor by eradicating wiring errors.
- Compact Solution: Traditional components, eat your heart out! Relay provides an impressively compact solution.
- Reprogrammable: Relay is as flexible as a gymnast! How so, you may ask? Well, control schemes can be altered with ease, enhancing versatility in operations.
- Reliability and Flexibility: Relay promises transferable programs, reduced programming times, and negligible debugging.
- Advanced Functions: From a simple repetitive action to complex data manipulation – Relay does it all and does it well!
Feature | Benefit |
---|---|
Communications: | Relay facilitates easy information exchange with interfaces, other PLCs, computers, enabling efficient data collection. |
Speed: | Relay has a quick response capability, a feature highly needed for many automated machines. |
Diagnostics: | Troubleshooting doesn’t have to be a hassle with Relay’s built-in diagnostics that help detect and correct problems. |
Relay Downsides
As we wait eagerly for the company to reveal specifics on the limitations and downsides of Relay; we’re firm believers that the pros trump any cons!
Relay Use Cases
Use Case 1: Industrial Control Systems
Relay is your go-to for tasks requiring repetitive, time-driven, and high-speed control operations; making it a popular choice for industrial control systems.
Use Case 2: Education
Want to lay a solid foundation for your electrical skills education? Relay offers an impressive electrical control teaching system, complete with 3D animations, interactive activities, and quizzes.
Use Case 3: Automation Systems
If you’re looking for a PLC that is compatible with many existing industrial automation systems, Relay shines bright. Its various machine controls are uniquely tailored to multiple scenarios, from traffic light sequencing to gate control.
IIoT
Delving into the paradigm of smart sensors, the Industrial Internet of Things (IIoT) transcends conventional industry processes.
IIoT Top Features
- Data collection, exchange, and analysis for enhanced efficiency.
- Predominantly used in manufacturing, utilities, and energy management, including oil & gas.
- Applicability in automotive industry for proactive maintenance & data gathering on potential maintenance issues.
- Employed in agriculture for soil nutrient and moisture data collection for optimal crop growth.
Enabled Features | Applications |
Predictive maintenance | Real-world IIoT deployment using smart robotics. |
Crucial device and patch management | Reduces system failures & enhances field services. |
Data Collection & Analysis | Improves facility management & customer satisfaction. |
IIoT Limitations
- Security risks with increased connectivity.
- Challenges in robust device and patch management.
IIoT Use Cases
Use case 1: Oil & Gas Industry.
IIoT brings forth a revolution in pipeline safety & operation, with Shell extracting 10{66f7997927a862c9f57ec7dffc6a2fe6d405caee7001dff533b976d48fe118b1} more oil & 5{66f7997927a862c9f57ec7dffc6a2fe6d405caee7001dff533b976d48fe118b1} more gas in smart oil fields compared to traditional ones using IIoT.
Use case 2: Smart Utilities
Smart utility grids embracing IIoT enhance energy balance, adaptability & lead to effective outage prevention.
Use case 3: ‘Smart Cities’
IIoT aids in comprehensive urban planning by providing planners with improved oversight & streamlined operations, which essentially bring ‘Smart Cities’ into existence.
RPA
Asserting its stance as a revolutionary tool, Robotic Process Automation (RPA) is a game-changing technology that allows software robots to mimic human actions in digital systems. Equipped with the capabilities to enhance enterprise efficiency and flexibility, RPA also improves employee satisfaction by eliminating the monotony of mundane tasks.
Top RPA Features
- RPA makes it possible to automate workflows involving legacy systems without APIs, virtual desktop infrastructures, or database access.
- The technology provides breakthrough solutions for finance, compliance, customer service, operations, and IT.
- RPA tools record user interactions with an app and create bots to trial user task performance, magnifying process efficacy.
- The integration of RPA with Artificial Intelligence and machine learning offers enhanced content context and process decision-making abilities.
Feature | Brief Explanation |
---|---|
Semi-structured Data Handling | The technology enables work with semi-structured or unstructured data, screen visualizations including virtual desktops, and even speech comprehension. |
Quick ROI | RPA yields swift, substantial return on investment with minimal upfront costs, hitting your profitability markers at lightning speed. |
RPA Limitations
- The initial process of analysis and engineering can be complex, requiring expertise.
- Maintenance, scaling, and seamless third-party integrations could potentially add to operational costs.
- Recurring costs are applicable as per the number and complexity of bots in deployment.
RPA Pricing
RPA software costs usually range between $5,000 to $15,000. This, however, is scalable, and costs for company-wide automation can run into millions depending on various factors such as vendor pricing, bot complexity, initial process analysis, engineering costs, third-party integrations, maintenance, and scaling costs.
RPA Use Cases
High Volume Tasks
RPA simplifies the automation of high-volume, repetitive, or rule-driven tasks in industries, freeing human resources for more complex activities.
Intelligent Process Automation
Integration of RPA with process mining breaks new ground in creating intelligent process automation, boosting organizational growth and strategic foresight.
Cognitive Tasks
Cognitive tasks requiring higher order AI skills are no longer out of reach with RPA technologies, pushing the envelope on enterprise capabilities.
GUI
In the vast digital sphere, GUI (Graphical User Interface) serves as a cardinal touchpoint that has greatly influenced how we engage with technology. It is a computer program instrumental in fostering communication between users and computers by employing symbols, visual metaphors, and pointing devices.
GUI Best Features
- An intuitive system simplifying computer operation making it more user-friendly.
- Standard computer interface largely adopted across the globe.
- The foundation of WIMP (Window, Icon, Menu, and Pointing device) paradigm that extends even into the gaming world.
Innovations | Involves contributions from innovators like Vannevar Bush, Douglas Engelbart, and Alan Kay. |
Evolution | Transitioned from command line interface to menu-dominant interface, finally arriving at GUI. |
Future-proof | Considers future needs with touch-sensitive LCDs, enhancing product longevity and reducing size. |
GUI Limitations
- Replacing electromechanical and optoelectronic elements with touch-sensitive LCD may pose risks for applications with potentially higher complexity.
- Adding LCD to existing products demands a level of redesign and adjustment which can be challenging.
GUI Use Cases
Use case 1
GUI plays a pivotal role in easing human-computer interaction and communication in devices. This is especially essential for businesses relying heavily on web applications and mobile applications, where a streamlined and intuitive UI is key to improving users’ overall experience.
Use case 2
For designers, artists, and creators, GUI provides an intuitive platform that ensures their focus stays on the creative process. By transforming intricate commands into visually interactive elements, it revolutionizes how creators engage with technology.
Use case 3
The gaming sector has also benefited greatly from the development of GUI. Employing the WIMP paradigm in game aesthetics and controls allows for a more immersive and interactive gaming experience. This has played a significant role in the global popularization of video games.
OIT
Standing as a testament to the innovation in control systems, stands the OIT, or Operator Interface Terminal. This entity provides for the read-write functionality of controller internal registers within a digitally controlled environment.
OIT Top Features
- Message Request Register (MRR): A continuous observer, it performs exclusive functions, dictating the display on the OIT screen, and can even delegate the task of content delivery to an optional serial printer.
- Multiple Language Support: OIT breaks language barriers, demonstrating versatility and inclusivity.
- Current Message Register (CMR): This component is the messenger of the contemporary happenings on the OIT screen, making it invaluable for chained sequences.
- Key coils: Split into Function key coils and Control key coils, they form the data transfer channel between the OIT and controller.
- Designed for resilience and longevity, the OIT offers control keys to facilitate monitoring by controller and register monitoring for memory checks, taking the power of control to the next level.
Feature | Use |
---|---|
Status Register | The mediator of information between OIT and controller, administering handshakes for messages, alarms and errors. |
Linear scaling on registers | Promises readability of operator data. |
ProControl Furnace Control System | Leverages OIT for PLC communication and delivers multilayer password protection. |
OIT Limitations
- With wired Ethernet TCP/IP taking precedence, the use of RS-232 as OIT network reduces. This switch in dominance can mean reconfiguration in some setups.
- In its quest for simplicity and user ease, the focus is shifting to flat-panel displays, pushing keypad operation, and text-only capability to the sidelines.
OIT Pricing
Boulder OIT offers a comprehensive suite ranging from Private cloud server at $115/month, Virtual Machine Management at $30/month and 24×7 support at $20/month. Also, it renders VM CPU at $85/month, VM Memory at $5/GB/month, and VM Storage at just $0.20/GB/month. For consultations, the service is priced at $133/hour and $266/hour post working hours.
OIT Use Cases
Use case 1
OIT comes to the fore in delivering temperature, time, pressure displays on ovens, autoclaves, and clean-in-place systems, ensuring a constant relay of critical information for optimal operation.
Use case 2
A beacon for manufacturing, OIT holds a majority stake,50{66f7997927a862c9f57ec7dffc6a2fe6d405caee7001dff533b976d48fe118b1} for both batch and continuous processing, proving effective also in the discreet manufacturing and continuous processing sectors.
Use case 3
From aiding in on-floor operations in robotics and warehousing, to redefining panel ergonomics, OIT holds the power to transform how industries operate and interact with their control systems.
ICS
An Industrial Control System (ICS) serves as an umbrella term for devices, systems, networks, and controls required for running and automating various industrial processes.
ICS Top Features
- Comprehensive Components: ICS environment embraces IT & Operational Technology (OT) variables, Programmable Logic Controller (PLC), Remote Terminal Unit (RTU), Control Loop, Human Machine Interface (HMI), Control Server, SCADA Server, Intelligent Electronic Device (IED) and Data Historian.
- Varieties: Includes Supervisory Control and Data Acquisition (SCADA) & Distributed Control Systems (DCS).
- Communication Protocols: Uses protocols like Process Field Bus (PROFIBUS), Distributed Network Protocol (DNP3), Modbus, and Open Platform Communication (OPC).
SCADA | DCS |
---|---|
Largely used for monitoring and control over long distances, focusing on supervisory level control. | Primarily for controlling production systems within one location, using centralized supervisory control loop. |
Composed of devices like PLCs scattered across different sites | Lessens the impact of a single fault on the complete system. |
ICS Limitations
- Vulnerability: ICS are susceptible to targeted attacks, a menace exacerbated by a convergence of IT and OT and arrival of technologies like cloud computing, big data analytics, and IoT.
- Increased Cybersecurity Threats: IT/OT convergence leads to better integration and supply chain visibility but poses larger targets for cybercriminals.
ICS Use Cases
Use case 1 – Manufacturing
ICS, especially with DCS, is extensively utilized in the manufacturing industry. It offers centralized supervisory control, thus reducing system faults’ influence.
Use case 2 – Transportation
With devices like PLCs distributed at different locations, ICS can be particularly beneficial in remote process monitoring and control for the transportation industry.
Use case 3 – Energy and Water Treatment
In the sectors of energy and water treatment, ICS plays a crucial role by facilitating long-distance process monitoring and control via SCADA systems.
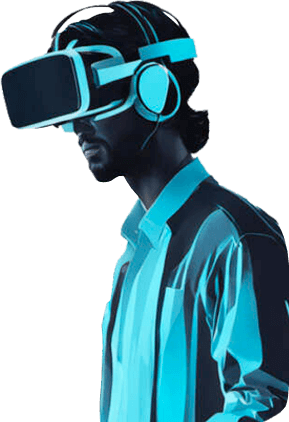