Navigating the Basics: PLC vs IIoT
For enhanced interconnectivity and data-driven automation in large-scale operations, IIoT excels with smart sensor technology. However, if your focus is on managing specific processes and maintaining cost-efficiency, PLCs remain a robust, tried-and-tested choice. Choose according to application needs and security considerations.
Key Differences Between PLC and IIoT
- PLCs are designed for controlling specific, repeatable processes, while IIoT systems are geared towards large-scale data analysis and predictive capabilities.
- PLCs have widespread standardisation, IEC 61131-3, easing understanding of programming language. In contrast, IIoT systems work with various protocols leading to interoperability but introducing complexity.
- PLC programming is, for the most part, reliant on a skilled workforce for troubleshooting, whereas IIoT offers remote monitoring and potential for autonomous error correction.
- IIoT presents higher potential risk for security breaches due to increased connectivity, though countermeasures like multifactor authentication and end-to-end encryption can be implemented.
Comparison | Programmable Logic Controllers (PLCs) | Industrial Internet of Things (IIoT) |
---|---|---|
Invention Era | 1960s | 21st Century |
Application Areas | Robotic arm in cars, air compressors, airport runway control, traffic signal control, smoke alarm control, textile equipment etc. | Manufacturing, energy management, utilities, oil & gas, automotive industry, agriculture, smart cities. |
Associated Technology | Data Highway by Allen-Bradley and Modbus by Modicon, Human-Machine Interface (HMI), ERP, MES systems, SCADA | Smart sensor-based system, 5G, Cloud computing, AI, machine learning |
Benefits | Flexibility, corrects errors, saves space, low cost, easy testing and troubleshooting. | Predictive maintenance, efficient field service, asset tracking, increased customer satisfaction, improved facility management. |
Challenges | Difficulty in troubleshooting, needs skilled workforce. | Security risks, device management & patch management. |
Functions | Monitors and records run-time data like machine productivity, operating temperature; Useful in start-stop processes, generating alarms during machine malfunctions. | Data collection, exchange & analysis for efficiency; Enables predictive maintenance, energy management & asset tracking. |
What Is PLCs (Programmable Logic Controllers) and Who’s It For?
PLCs or Programmable Logic Controllers are automated devices, integral in modern manufacturing processes. First invented in the 1960s, these controllers have evolved over time, becoming smaller and faster while embedding powerful capabilities. They are majorly employed to streamline and automate industrial and manufacturing actions, hence ideal for anyone in the manufacturing sector.
Developed to replace cumbersome hardwired relays and timers, PLCs have metamorphosed into sophisticated devices. They have become indispensable in a wide range of application areas such as automotive production, airport runway control, and textile equipment, among others.
Pros of PLCs
- Flexibility and adaptability in diverse applications.
- Reduces operation downtime and enhances efficiency.
- Monitors and records run-time data, useful in process management.
Cons of PLCs
- Require skilled workforce for operation and maintenance.
- Can be challenging to troubleshoot.
What Is IIoT (Industrial Internet of Things) and Who’s It For?
IIoT, or Industrial Internet of Things, is a smart system built on sensor technology; it’s a game-changer in industries such as manufacturing, energy management, and oil & gas. By collecting, exchanging, and analyzing data in real-time, IIoT enables predictive maintenance, enhanced field service, superior asset tracking, and efficient energy management, making it invaluable for industries involved in large-scale processes and operations.
With accelerated advancements in cloud computing, AI, and machine learning, the future of IIoT is intricately linked to the advent of Industry 4.0. The IIoT market is poised for exponential growth, projected to surge from $221.7 billion in 2022 to $516.6 billion by 2028.
Pros of IIoT
- Boosts operational efficiency and improves financial outcomes.
- Enables predictive maintenance and efficient field service.
- Innovates smart utility grids for better energy balance and outage prevention.
Cons of IIoT
- Potential security risks due to increased connectivity.
- Challenges in managing and updating IIoT devices.
Decoding the Choice: PLC vs IIoT
In the grand tech duel of PLC and IIoT, our verdict depends on the job you need done.
For Manufacturing Enthusiasts
When precision and customization top your list, PLCs stand unrivaled. The capacity to handle complex machinery, coupled with a rich history of adaptability and evolution, makes PLCs a solid choice. PLCs’ flexibility, cost-effectiveness, and error correction continue to serve manufacturing sectors seamlessly.
Oil & Gas Experts
In the intricate world of oil and gas, where pipeline safety is paramount, IIoT stars. Its application in real-time data collection for potential maintenance issues and pipeline leakage prevention has proved invaluable, thereby simplifying a traditionally complex sector.
Smart City Planners
For those advocating for smarter, smoother cities, IIoT leads the path. Its utility in areas such as automation, passenger navigation, and security enhancement brings smart city dreams closer to reality. The connectivity IIoT brings about supports city planners in overseeing operations seamlessly.
The Gordian knot of PLC vs IIoT unravels with your specific needs. If you need a stalwart for intricate processes, PLCs excel. If real-time data collection and enhanced connectivity empower your industry, IIoT paves the way.
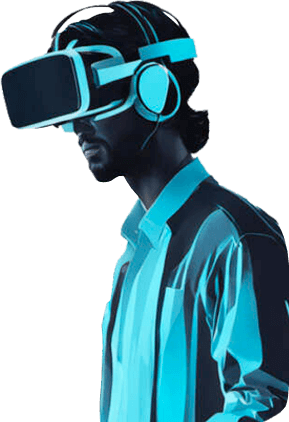