Deciding Between PLC vs Microcontroller
For firms seeking process automation, the Programmable Logic Controller (PLC) is king, with unrivaled power and robustness, making it fit for larger-scale operations. If you need an economical and energy-efficient option for discrete tasks, banking on Microcontrollers would be wise.
Key Differences Between PLCs and Microcontrollers
- PLCs: Integral in large-scale manufacturing and process automation, utilizing standardized software. Greater in size and cost yet astonishingly robust.
- Microcontrollers: Compact, energy-efficient ICs governing specific embedded systems operations. Ideal for discrete tasks in smaller devices.
- Memory and I/O: PLC involves larger, dedicated modules, while microcontrollers integrate these onto a single chip.
- Industry application: PLCs dominate in robustness-demanding sectors like automation; Microcontrollers excel in automotive, home appliances, and similar areas.
- Environmental resilience: PLCs are generally more resilient to tough industrial environments. Microcontrollers, however, are also designed to withstand varying conditions.
Comparison | Programmable Logic Controllers (PLCs) | Microcontrollers |
---|---|---|
Definition | Automate many processes; vital in manufacturing. | Compact integrated circuit, governs specific operation in embedded system. |
Key Components | CPU with processor, memory, Input/Output modules, power supply. | Processor (CPU), memory, I/O peripherals. |
First Invention | First developed by General Motors as ‘Standard Machine Controller’ in 1968. | Created by TI engineers Gary Boone and Michael Cochran in 1971. |
Advanced Features | PLCs now integrated with ERP, MES systems, and SCADA, aiding manufacturing efficiency. | Includes ADC and DAC, enabling efficient communication with external devices. |
Programming Language/s | Ladder Logic, Flow Charts, Structured Text, Instruction List. | C, Python, JavaScript. |
Application Areas | Used in control systems like automotive assembly line, air compressors, airport runway control, etc. | Used in embedded systems like vehicles, robots, office machines, and even home appliances. |
Disadvantages | Difficult in troubleshooting, requires skilled workforce. | While it is robust and versatile, it is less sophisticated than SoCs or microprocessors. |
What Is Programmable Logic Controllers (PLCs) and Who’s It For?
An automated solution catalyst to streamline manufacturing processes, Programmable Logic Controllers (PLCs) are compact, intelligent control units that monitor multifarious complex industrial systems while also being nimble enough to adapt. Birthed from a vision to supersede antiquated hardwired relay systems back in the 1960s, the PLC is known for its versatility in the size spectrum, packing affordable microprocessors. Process Solutions, a name synonymous with superior durability and efficiency, prides itself on more than three decades of experience in the realm of PLCs.
A PLC’s scope of operation is broad, spanning a diverse range of applications, be it controlling the nimble robotic arms assembling vehicles or monitoring sophisticated air compressors. Its flexibility, capacity for error correction, ease of testing, and conservation of space, however, earmark this technology as the favored solution for industry professionals aiming for streamlined operations.
Pros of Programmable Logic Controllers
- Easily programmable using relay ladder logic.
- Integrated with ERP, MES systems, SCADA for advanced operational efficiency.
- Rapid development due to introduction of data highway and Modbus.
- Wide application areas from automotive to textile.
- High flexibility, error correction capability, space-saving, and cost saving.
Cons of Programmable Logic Controllers
- Troubleshooting might be difficult.
- Requires skilled workforce to operate.
What Is Microcontroller and Who’s It For?
A confluence of compactness and versatility, a Microcontroller is a comprehensive integrated circuit, central to the command of specific operations in embedded systems. Single-chip housing for a processor, memory, and input/output peripherals, the Microcontroller, or the ’embedded controller’, dethrones the need for a complex front-end operating system (OS). Trusted across a spectrum of applications from routine office machines to intricate medical devices, microcontrollers are the lynchpin of fluid operations.
Typically furnished with an Analog to Digital Converter (ADC) and a Digital to Analog Converter (DAC), microcontrollers enjoy industry-wide usage. Whether it’s building an intelligent automation system or devising smart energy solutions, microcontrollers leverage their robust structure, rich features, and economic fame to command an influential presence across the technology landscape.
Pros of Microcontrollers
- Economical and power-efficient as compared to microprocessors.
- Embedded with multiple functions improving compactness.
- Available in different memory types, instructions, and architectures.
- Applicable in various industries.
Cons of Microcontrollers
- Fewer capabilities compared to Systems on Chip (SoCs).
- Selection can be complex due to various tech considerations.
PLC or Microcontroller – Which Takes the Technological Edge?
In the realm of technology, the question of whether to choose a Programmable Logic Controller (PLC) or a Microcontroller often arises. The answer, however, hinges upon your specific needs and the nuances of your project.
Industrial Automation Experts
For specialists in industrial automation, we lean towards PLCs. With a rich history being designed explicitly for automation, PLCs offer advanced capabilities thanks to advancements in processor and memory technology. They perform optimally in applications necessitating expensive data acquisition systems by replacing large relay banks, which eases maintenance and understanding of programming language.
Embedded Systems Developers
If you’re an embedded systems developer, your inclination should gravitate towards Microcontrollers. Their compact design hosting processor, memory, and input/output peripherals in a single chip make them the go-to option for controlling specific operations in an embedded system. Plus, their hardiness in tough conditions enhance their appeal.
IoT Enthusiasts
The IoT enthusiasts are most likely to derive significant benefits from Microcontrollers. Their minimal power consumption, compactness, and affordability give them an edge in IoT applications, especially where power and cost constraints come into play.
Deciding between PLCs and Microcontrollers boils down to your project specifics and their fittingness into those perimeters. PLCs, mentioned for automation dominance, are hard to overlook. However, for embedded systems and IoT applications, Microcontrollers prove their worth. Your decision should be founded on aligning technological capabilities with project requirements.
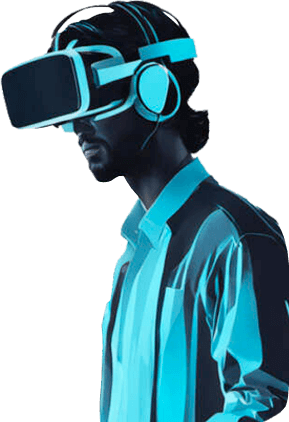