First Impressions: PLC vs RPA
When comparing Programmable Logic Controllers (PLCs) with Robotic Process Automation (RPA), PLCs take precedence in manufacturing and hardware control scenarios, where precise and constant control is required. However, RPA is a stronger choice for business processes, particularly where sizable amounts of data and repetitive tasks are involved.
Key Differences Between PLC and RPA
- Coding: PLCs utilize Ladder Logic, a visual representation of Boolean Logic, for easy understanding by engineers. RPA automates tasks through software, requiring no specific coding skills.
- Application: PLCs excel in controlling heavy machinery and equipment, used extensively in manufacturing. RPA predominantly caters to business process automation across diverse industries.
- Integration: While PLCs integrate with ERP and SCADA systems, RPA melds seamlessly with AI and machine learning for improved cognitive functions.
- Cost: PLC affordability varies based on the functionality, with a standard PLC system being less costly than an RPA system. RPA software costs can mount up into millions, depending on the scale of automation.
Comparison | PLCs | RPA |
---|---|---|
Description | Digital device with a programmable memory for the internal storage of user-oriented instructions for implementing specific functions | Technology enabling easy deployment of software robots emulating human’s actions interacting with digital systems |
Key Applications | Robotic arm in cars, air compressors, airport runway control, traffic signal control, smoke alarm control, textile equipment | Workflow automation involving legacy systems, virtual desktop infrastructures (VDIs), or database access |
Primary Benefits | Flexibility, corrects errors, saves space, low cost, easy testing and troubleshooting | RPA bolsters productivity, efficiency, resilience in enterprises, and generates swift, significant return on investment (ROI) with minimal upfront investment |
Core Components | CPU with processor, memory, Input/Output modules, power supply. Optional- additional components like network interfaces | RPA bots that can interact with applications, enter data, perform tasks, and transfer data as per workflows |
Key Innovations/Advancements | Integration with ERP, MES systems, SCADA, aiding manufacturing operations’ efficiency, introduction of many advanced PLC features: vision system integration, motion control, synchronized support for multiple communication protocols | Integration of RPA with AI and machine learning offers enhanced content context via reading text with OCR, extracting entities using NLP |
Challenges/Disadvantages | Difficulty in troubleshooting, needs skilled workforce | The cost which can range from $5,000 to $15,000. A business could spend millions for company-wide automation |
What Is Programmable Logic Controllers (PLCs) and Who’s It For?
Programmable Logic Controllers (PLCs) are powerful tools keyed to automate industrial processes. Inherited from the 1960s as a compact, faster, and more potent alternative to hardwired relays and timers, PLCs modernized with processor and memory tech advancements. Ideal for manufacturing operations, they got metal and premium with integrated software like ERP, MES systems, and SCADA, enhancing efficiency and performance.
Manufacturing industries heavily rely on PLCs for ensuring their machines function optimally. This technology also serves in robotic arm in cars, air compressors, airport runway control, traffic signal control, smoke alarm control, and textile equipment manufacturing.
Pros of Programmable Logic Controllers (PLCs)
- Flexibility and compatibility with a broad spectrum of systems
- Reduction in machine downtime and errors
- Space-saving due to compact size
- Eases testing and troubleshooting
- Cheaper than other hardware systems
Cons of Programmable Logic Controllers (PLCs)
- Troubleshooting can be complex.
- Requires a skilled workforce for operation
What Is Robotic Process Automation (RPA) and Who’s It For?
Robotic Process Automation (RPA) encompasses technology facilitating software robots to mirror human interactions with digital systems. Born to automate workflows and augment profitability, RPA is game-changing, particularly for enterprises running legacy systems that lack APIs, virtual desktop infrastructures (VDIs), or database access.
RPA is a boon for sectors including finance, compliance, customer service, operations, and IT, delivering significant ROI with slight upfront investment. Deploying RPA results in enterprise agility, amplified productivity, efficiency, and resilience.
Pros of Robotic Process Automation (RPA)
- Enhances productivity and efficiency
- Reduces costs and streamlines processing
- Improves customer experiences
- Non-disruptive, scalable, and ready for enterprises
Cons of Robotic Process Automation (RPA)
- Costs could be significant with company-wide automation
- Requires ongoing maintenance, support, and occasional scaling
A Ruling on the PLC vs RPA Debate
In an era where technology decides efficiency, making an informed choice between PLCs and RPAs is paramount.
Manufacturing and Industrial Automation
With PLCs being integral in automating processes and heavily employed in manufacturing, this audience would find the PLC most fitting. Their historical roots in this field, their integrated use with SCADA and ERP systems, and their specialization for start-stop processes are undeniable merits. Furthermore,
- Process Solutions’ high-quality control systems,
- Rapid development by Allan-Bradley and Modicon,
- and the newer programming languages,
provoke a lean toward PLCs.
Enterprises Seeking Cost-Effective Efficiency
For enterprises chasing profit and flexibility, the RPA shines through. It eliminates monotonous tasks, extends to workflows involving legacy systems, and offers tremendous ROI. Moreover, the fact that
- 63{66f7997927a862c9f57ec7dffc6a2fe6d405caee7001dff533b976d48fe118b1} of global executives earmark RPA as a vital part of digital transformation,
- RPA doesn’t disrupt systems,
- and it allows interaction with semi-structured or unstructured data,
justifies the leaning toward RPAs.
Large-Scale Automation Users
Entities working with high-volume, repeatable processes or cognitive tasks will find the RPA more beneficial. Given RPAs’ ability to reduce costs, streamline processing and improve customer experiences, the choice becomes clear. Plus, the integration of RPA with AI and process mining makes it an indispensable tool for automation.
When choosing between PLCs and RPAs, consider the intended application. For manufacturing and industrial controls, PLCs excel. However, businesses wanting task automation across various departments may find the RPA more suitable for its versatility and return on investment.
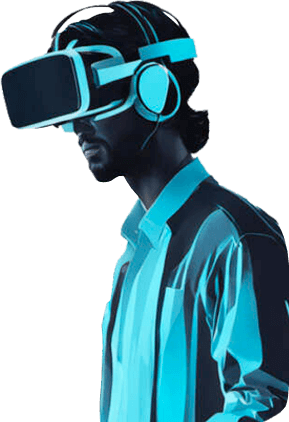