Getting to the Heart of SCADA vs PLC
PLCs provide advantages in cost-effectiveness, compactness, and adaptability, ideal for industries requiring precise control and simplifying maintenance and troubleshooting. Alternatively, SCADA thrives better in large-scale production environments, yielding centralized control and extended data trend analysis, crucial for sectors like water control, energy, and transportation.
Key Differences Between SCADA and PLC
- Scale of Operation: SCADA facilitates control on a full network, while PLCs target specific processes.
- Data Analysis: SCADA enables real-time data gathering and trending, absent in PLCs.
- System Components: PLCs majorly include CPU, power supply, and I/O modules. SCADA comprises RTUs, sensors, HMI, and control relays.
- Cybersecurity: SCADA’s broader connectivity presents more cybersecurity threats than PLCs.
- Cost: Typically, PLCs entail less cost in the long run compared to SCADA.
- Industries Served: SCADA’s reach spans energy, waste control, and telecom sectors, while PLCs are prevalent in manufacturing sectors.
Comparison | SCADA | PLCs |
---|---|---|
Definition | Supervisory Control and Data Acquisition, computer application that monitors, controls plant or equipment at supervisory level. | Programmable Logic Controllers, automate many processes; vital in manufacturing. |
Components | Remote Terminal Unit (RTU), sensors, control relays, SCADA master units, communication channels, Human-Machine Interface (HMI), controllers, software. | CPU with processor, memory, Input/Output modules, power supply; optional-additional components like network interfaces. |
Application Areas | Used in industries including industrial plants, water and waste control, energy, oil and gas refining, transportation, telecom. | Robotic arm in cars, air compressors, airport runway control, traffic signal control, smoke alarm control, textile equipment etc. |
Evolution | Early SCADA systems were monolithic systems, later evolved to distributed and networked SCADA systems. Now incorporating SQL databases, rapid application development (RAD) capabilities. Future lies with 5G networks, quantum computing, edge computing, artificial intelligence, and machine learning. | First PLC developed in 1968 as ‘Standard Machine Controller’. PLCs became smaller, faster, more powerful; helped in paving way for Internet big data, artificial intelligence on factory floor in 21st century. PLCs now integrated with ERP, MES systems, SCADA; languages developed include Flow Charts, Structured Text, Instruction List. |
Risks | Has Cybersecurity concerns with more connected and integrated systems. | Difficulty in troubleshooting, needs skilled workforce. |
Benefits | Modern SCADA are scalable, interoperable, widely supported, improve accessibility to data and controls. | PLCs: flexibility, corrects errors, saves space, low cost, easy testing and troubleshooting. |
What Is SCADA and Who’s It For?
SCADA, short for Supervisory Control and Data Acquisition, is a high-level control system aimed at automating complex industrial processes. It’s designed to collect real-time data, log events, and detect/correct issues within plant and equipment setups. It’s particularly indispensable in sectors like waste control, energy, industrial plants, oil and gas refining, and transportation. Notable features include networks, controllers, Input/output signal hardware, Human-Machine Interface (HMI), database, and software.
Newer SCADA systems embrace modern technologies like SQL databases, artificial intelligence, machine learning, and more recently, quantum computing and 5G networks. This digital leap, however, poses cybersecurity issues owing to system integration and connectedness.
Pros of SCADA
- Automates complex industrial processes
- Improves real-time data monitoring and processing
- Predicts and mitigate faults
- Integrates AI and Machine Learning for enhanced performance
Cons of SCADA
- Increased cybersecurity risk due to system integration
- Scalability and interoperability issues with legacy systems
What Is PLC and Who’s It For?
Programmable Logic Controllers, or PLCs, are devices designed to automate processes, particularly in the manufacturing environment. The evolution of PLCs has been monumental, moving from suitcase-sized ingeniously interconnected relay banks in the 60s to compact yet mighty devices embracing big data and artificial intelligence.
Current PLCs are incorporated with ERP and SCADA systems, improving manufacturing operations’ efficiency. They are critical in applications that required costly data acquisition systems, thanks to the decreasing cost of solid-state memory.
Pros of PLC
- Boosts manufacturing efficiency
- Allows integration with ERP, SCADA systems
- Supports diverse programming languages
- Improves machine monitoring and troubleshooting
Cons of PLC
- Demand for skilled workers
- Troubleshooting can be challenging
SCADA or PLC – The Tech-Heavy Decision
Undeniably, both SCADA and PLC prove instrumental in various industry applications, thereby necessitating a prudent decision, predominantly audience-specific.
Large Scale Industrial Over-Seers
SCADA’s prowess in centralized control and automation of industrial processes merits it as an ideal solution for industries including oil & gas, energy, telecom, water & waste control. Prospective developments in AI, edge computing, and 5G integration place SCADA on an upward trajectory poised for returning substantial benefits. However, cybersecurity concerns resurfacing with integrated connectivity tend to undermine SCADA’s supremacy.
Compact Complex Controllers
Emerging out as an ace in automating intricate operations, PLC serves efficiently in manufacturing setups. Smaller, faster, yet formidable when compared to its 1960s peers, PLC’s interplay with ERP, MES systems, and SCADA accelerates operational efficacy. PLC’s diagnostic abilities enhance troubleshooting, albeit demanding a proficient workforce.
Future Ready Industries
Brace for an exciting, tech-forward future with SCADA’s envisioned inclusion of 5G networks and quantum computing, whereas PLC’s promise lay in the incorporation of advanced features like vision system integration and motion control. However, the sophistication comes with corresponding cybersecurity and workforce proficiency concerns.
In the SCADA vs PLC showdown, while SCADA excels in centralized control for vast industrial processes, PLC’s strength lies in automating complex operations within compact environments. However, audience-specific needs and a thorough analysis of benefits, complexities, and future scope largely dictate the optimal choice.
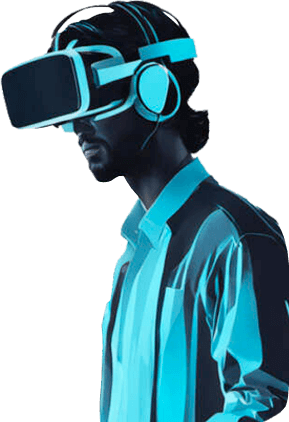